Inverter performance – or lack thereof – is the number one factor in the profitability of a solar asset.
Wood Mackenzie has predicted that premature inverter failure will occur in 36 GW of solar assets by 2025. It is clear that asset owners need reliable, high-performing multifunctional inverters. Yet the industry has long struggled with establishing standards for inverter technical due diligence.
Investors and asset owners can leverage independent inverter testing to avoid the high cost of equipment that must be repaired or replaced prematurely – just as they already do with PV modules.
One reason PV modules have become more efficient and reliable over the past decade is the wide availability of empirical data obtained through independent testing. Developers and financiers have established strict PV module testing and data requirements so that they can select quality products and build more accurate performance and financial models. The same process can and should applied to inverters.
Inverter Failure and Underperformance
In the very early days of solar energy development, inverters served one function: converting DC energy from PV modules into AC energy. Over time, inverter manufacturers have been pushed to incorporate more functionality and to act as the central communication hub for PV systems, such as:
- Maximizing power output
- Interfacing and supporting the utility grid
- Reporting system production
- Ensuring safe PV system operation
- Interfacing with other communications devices
- Integrating with batteries
As inverters are burdened with more tasks within a PV system, the number of internal components and software/firmware requirements have also increased. To learn more about this trend, download PVEL’s 2019 PV Inverter Scorecard. Note that while the next edition of this Scorecard has not yet been released, the trends discussed in the 2019 report remain relevant today.
Here’s the bottom line: inverters today contain more parts, more potential failure modes and more financial risks for asset owners. In particular, the Department of Energy has found that capacitors and printed circuit boards are responsible for many inverter issues observed in the field. Additional capacitors and circuit board and subsystem components means more opportunities for failure.
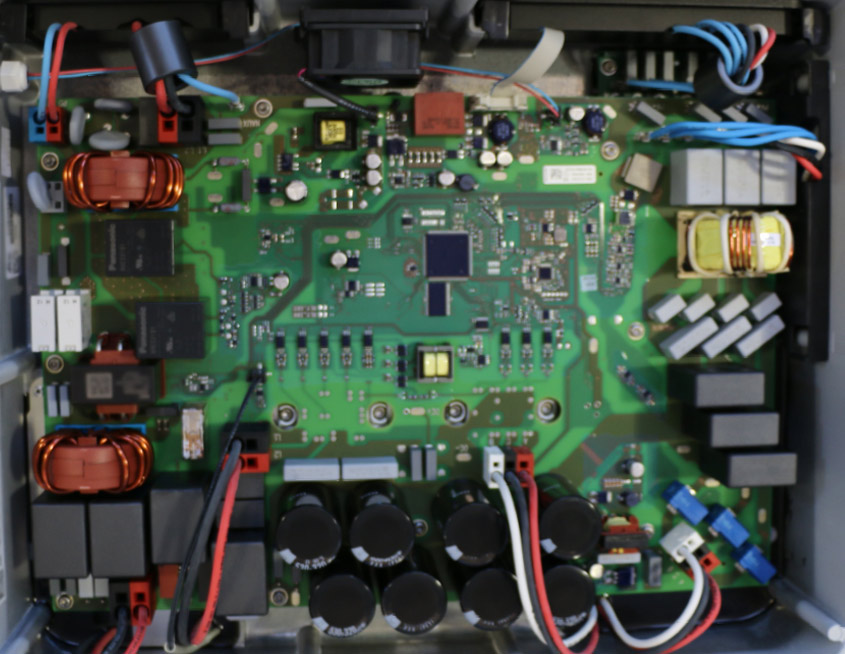
Above: the inside of an inverter. Inverters today are comprised of thousands of internal components.
Common problems with inverters, which are discussed in detail in our PV Inverter Scorecard, include:
- Overheating
- Failure to interface with the grid
- System-level communications issues
- Monitoring and reporting outages
- Nuisance tripping
- Component wear-out
- Power de-rating
Inverters are responsible for the majority of service calls associated with PV systems, and inverter outages, downtime and maintenance are a significant part of owner costs. For example, the following was reported in a 2019 paper published by NREL:
“In one 27-month study, module failures accounted for only 5% of total energy losses, whereas inverter failures accounted for 36% of lost energy during the same period”
(NREL)
Given that inverters can have outsize impact on energy loss, inverter diligence is just as important as PV module diligence. For a project to meet its energy yield and financial targets, both pieces of equipment must operate as expected.
However, industry research shows that inverters and power electronics rarely perform according to their datasheet specifications in the field. When inverters do not fail outright, but rather perform below expectations, the system still produces less energy and will underperform financially. A failure in the inverter’s ability to identify and report electrical arcs, which are more likely to occur as systems age and materials degrade, will also undermine safety at the site.
As inverters provide even more functionality and manufacturers are pressured to reduce costs, there is a tradeoff in reliability and lifespan. The push for cheaper power conversion equipment that can “do it all” sometimes juxtaposes the need for reliability. When asset owners and investors lack quality data from independent inverter testing, they often choose products based on brand name, cheaper price point and datasheet promises. This is exactly the same unsophisticated way PV modules were selected ten years ago.
Inverter Technical Due Diligence Lags Behind Modules
In the early days of solar production, PV modules contributed a much greater share of total system costs than PV inverters. When PV Evolution Labs (PVEL) published its first Product Qualification Program (PQP) for PV modules in 2012, PV modules cost $0.75 per watt. Prices for monofacial modules today are as low as $0.27 cents per watt.
Thanks in part to these falling module costs, inverters now make up a larger share of the total system cost. According to NREL’s research, inverters and associated power electronics constitute 8-12% of the total lifetime PV cost. However rigorous inverter testing that would yield predictive longterm performance results is often skipped. Buyers today have relied on certifications, brand names and warranties to qualify inverters.
Field observations of inverter failure prove that this safety- and commercially-, rather than technically-, driven diligence process does not protect asset owners:
- Certification tests are primarily designed to identify safety issues during the pre-production development of the products
- When underperformance and other issues arise for fielded systems, manufacturers often seek to address them through software updates, which may impact critical functionality.
- Manufacturer insolvency and market exits can invalidate warranties or make them extremely difficult to pursue.
- Replacement products may not be available due to phasing out of products in support of rapid technological advancements, but using those newer, more technically advanced products can result in voltage mismatch that forces the owner to reconfigure the entire PV system.
Inverter Testing Protects Asset Owners and Investors
PVEL is the only independent laboratory that offers PV inverter and power electronics testing designed for the global downstream solar industry through our Product Qualification Program (PQP). Our PV Inverter PQP was first developed in 2014, and we recently established our new inverter test center in South San Francisco to increase PQP testing throughput and capacity. It includes a standardized sequence of tests across five key categories:
1. Passive Chamber Testing
Exposes products to environmental stresses to evaluate their construction, design and susceptibility to moisture ingress to identify mechanical and electro-mechanical defects.
2. Thermal Performance Characterization
Evaluates the performance of products across the manufacturer’s specified operational temperature windows to characterize the impact of thermal derating as well as electromechanical fatigue on long-term reliability and energy yield.
3. Performance Testing: Efficiency
Analyzes the two core functions of inverters, converting DC to AC energy and interconnecting with the utility grid, to validate that products will perform as specified when deployed in the field.
4. Performance Testing: Operational Window
Measures product performance as AC output and DC input fluctuate in order to provide system design insights, identify products that are susceptible to nuisance tripping and inform financial and energy yield models for interconnected stringing configurations and .OND file estimates.
5. Field Testing
Evaluates the likelihood that products will operate as intended once fielded and identifies issues such as arc faults nuisance trip susceptibility which is fundamental to the economic success of certain PV systems.
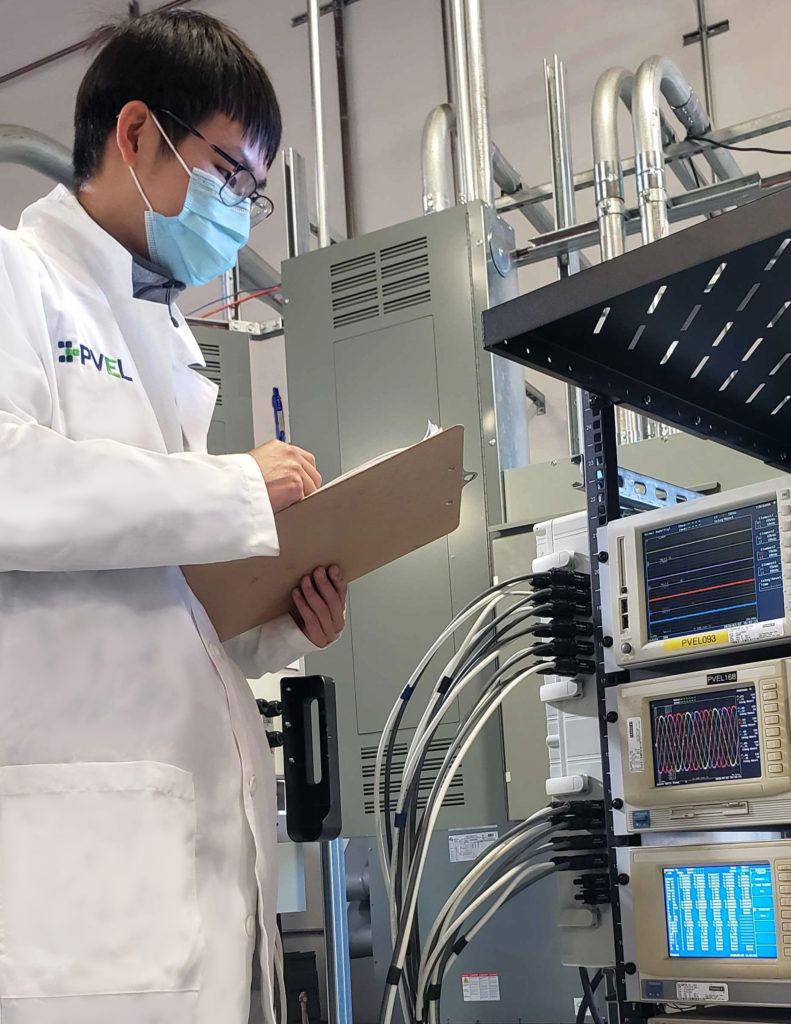
Above: PV inverter testing at PVEL
The PVEL PV Inverter PQP provides buyers with consistent benchmarking data. Our reports, which are complimentary for downstream companies, enable empirical, leveled comparisons of commercially available PV inverter products. Finally, PQP test results help investors and asset owners build more robust and accurate models to determine which products will meet their energy yield and financial performance expectations.
It is an industry standard to require independent testing for PV modules as a prerequisite to purchase. It is time for project stakeholders to demand the same for inverters.
Learn more about PVEL’s Power Pack Product Qualification Program for inverters:
This post was updated in July 2021.