American PV module manufacturing is experiencing a renaissance as U.S.-based companies ramp up domestic production and international companies establish local factories. Although the end of the exclusion of bifacial PV modules from the Section 201 tariffs could increase enthusiasm for American PV module manufacturing, there is still a lot of uncertainty around trade policy. By now the entire solar industry knows that tariffs can fluctuate dramatically and that these rapid rate changes can make profitable projects unviable. Investing in local capacity may prove to be a smart investment, especially for manufacturers headquartered outside of the U.S.
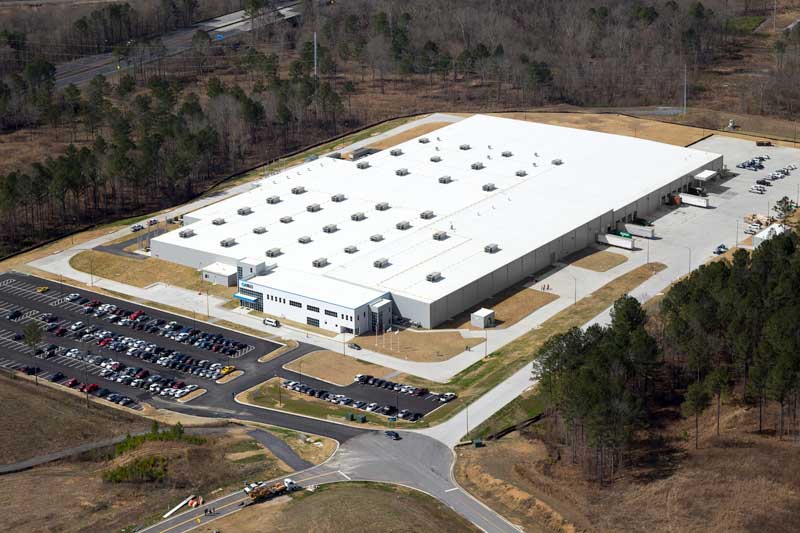
Q CELLS’ new factory in Dalton, GA (Image source: Q CELLS)
However, the country of origin of a PV module does not drive quality, performance or reliability. The bill of materials, production processes, and employees are the factors that matter. Even if a supplier produces high quality PV modules at other locations, it is critical to thoroughly vet the products coming out of any new manufacturing facility.
Why Manufacture PV Modules in Dalton?
Q CELLS is one of several PV module suppliers that have recently established U.S. manufacturing operations. Their new factory is located in Dalton, Georgia, also known as the Carpet Capital of the World because of the region’s high concentration of carpet factories.
The connection between carpets and PV modules wasn’t obvious at first. Then I learned that carpet production is fairly automated. Most workers monitor production via computers, much like their counterparts in modern PV module factories. (Learn more in this story from the New York Times.)
The Dalton factory will ultimately create about 650 new jobs in the area. Locating the new facility in a region where the local population has transferrable skills may prove advantageous for Q CELLS. While line managers and operators from Q CELLS’ Korean operations came to Dalton to help set up the factory and train the new team, the primary workforce is local. The company took care to note that its team was committed to building a workplace culture in the U.S. that reflected its high quality manufacturing practices in Korea.
Setting Up A Factory in Record Time
According to Q CELLS, its new 300,000 square foot factory is the largest in the Western Hemisphere. The massive operation was up and running in less than a year – the factory’s location was first announced on May 30, 2018 and modules were rolling off the production line by February 28, 2019. I attended the factory’s grand opening on September 20, 2019.
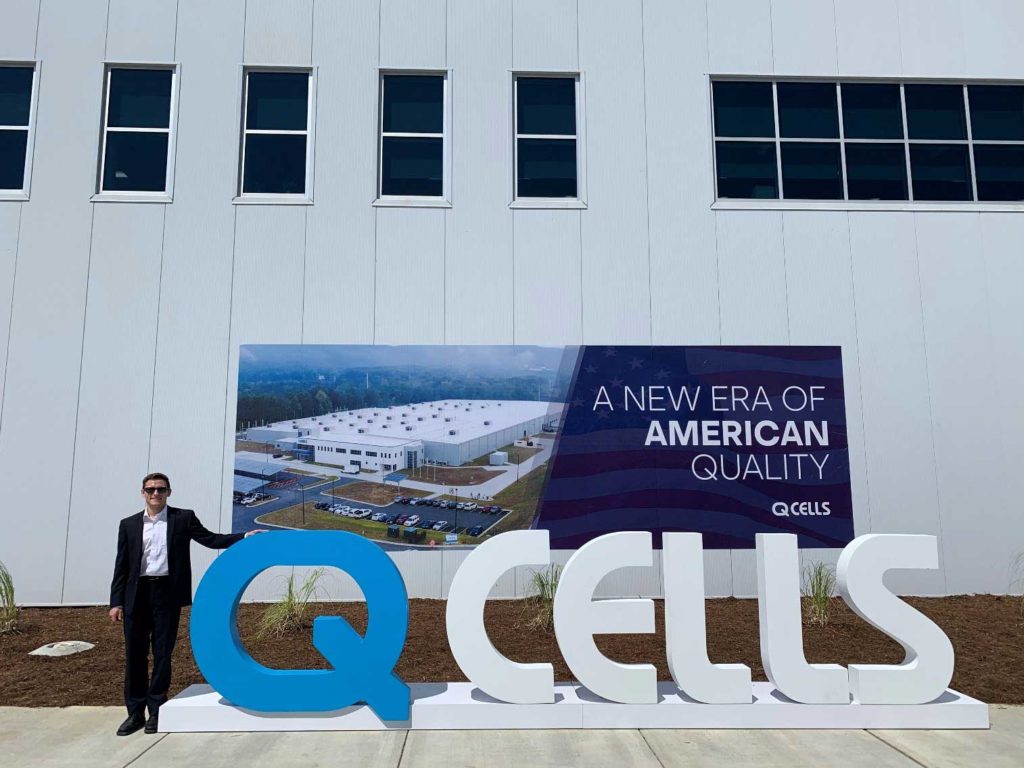
Soaking up some solar energy on a peachy day at the new Q CELLS factory in Dalton, GA
The factory has 1.7 GW of nameplate capacity and output modules are all intended for the U.S. market. Three fully automated lines are operating around the clock, seven days a week. The company is already using what it calls “artificial intelligence” to screen for defects during points in production.
While promising in many ways, it is important to note that neither artificial intelligence nor advanced machine learning-based inspection processes can guarantee defect-free modules. Like any quality control checks, these processes must be implemented correctly to succeed. If manufacturing equipment and inspection algorithms are not regularly calibrated and validated, serious problems may go undetected. At PVEL, we recommend that operator inspection remains a part of the process. A human eye should always verify product quality at key production steps.
On a local level, the opening of this facility represents a big win for the state of Georgia. At the ribbon-cutting ceremony, Governor Brian Kemp spoke at length about the Peach State’s enthusiasm for clean energy, which, when combined with its skilled local workforce and business-friendly environment, provided ideal conditions for the development of the factory. In his first international trip after his re-election, Governor Kemp went to Seoul to meet with Q CELLS CEO Charles Kim. Just over a year later, Kim and Kemp stood side-by-side to cut the ribbon to mark the grand opening of Q CELLS’ new hallmark factory.
Interested in PV module testing?
Explore tests for LeTID, backsheet durability, microcrack susceptibility and more in our Product Qualification Program for PV modules.