From the stock market to the grocery market, the coronavirus is disrupting daily life around the world. Solar industry veterans know how to adapt to uncertain regulatory environments, evolving tariff regimes and even novel PV module degradation modes most of the time. But the entire globe has never faced a situation like this before. At PV Evolution Labs (PVEL), we’re hearing mounting concerns about supply chain and construction disruption from our downstream partners. Here’s an overview of their top questions so far:
- Is there a shortage of subcomponents for PV equipment? Are suppliers now forced to use low-quality and/or untested components?
- My supplier suddenly wants to change factories. Can I trust the new facility to produce the same quality product?
- My selected factory was closed, now they’re open and working double-time to complete orders. Can they maintain quality standards with such an aggressive production schedule?
- Will construction slowdowns lead to a PV module oversupply – and ultimately price drops? Should I wait to purchase?
- Due to permitting and interconnection application delays, we’re rushed to complete our project in order to hit regulatory incentive deadlines. How can I ensure that my system is properly installed and the equipment is free of handling damage?
These concerns are all valid, but panicking will not ensure quality – and PVEL’s toolbox of procurement risk mitigation tactics is as powerful as it was before the coronavirus.
In this article, I will explain how solar project developers, investors and asset owners can follow tried and true technical best practices to protect their financial returns.
Changing Bills of Materials
Results from over ten years of testing at PVEL across 350+ bills of materials (BOMs) show that specific components dramatically impact product performance and reliability. For example, using low quality backsheets in PV modules can result in moisture ingress that causes power losses and safety issues over time. Using a DC bus capacitator that is sensitive to high temperatures can cause an inverter to fail prematurely.
While we’re hearing many questions about BOM substitution due to coronavirus-related upstream supply constraints, it has not been a major problem – yet. Most Asian factories had sufficient buffer stock on hand prior to factory closures, so they did not experience significant, long-term component shortages. In a recent interview addressing manufacturing in China, Andy Klump of Clean Energy Associates noted that Hubei Province, the center of the coronavirus outbreak in China, is not a major PV manufacturing hub, so the fallout was more limited for solar than other industries. Ian Gregory, Managing Director of PI Berlin North America, shared in a recent conversation that manufacturers have changed materials in response to shortages and are seeking to use older inventory to keep production going.
While the extent of supply chain impacts is not fully understood, we do know that coronavirus is affecting every country and economy where solar components are manufactured. This may present serious problems for buyers.
We recommend that developers proactively communicate with suppliers to prevent potential issues. If a supplier asks to change a BOM component, the developer can require additional testing per PVEL guidelines. Our team will work with the manufacturer to qualify the altered BOM.
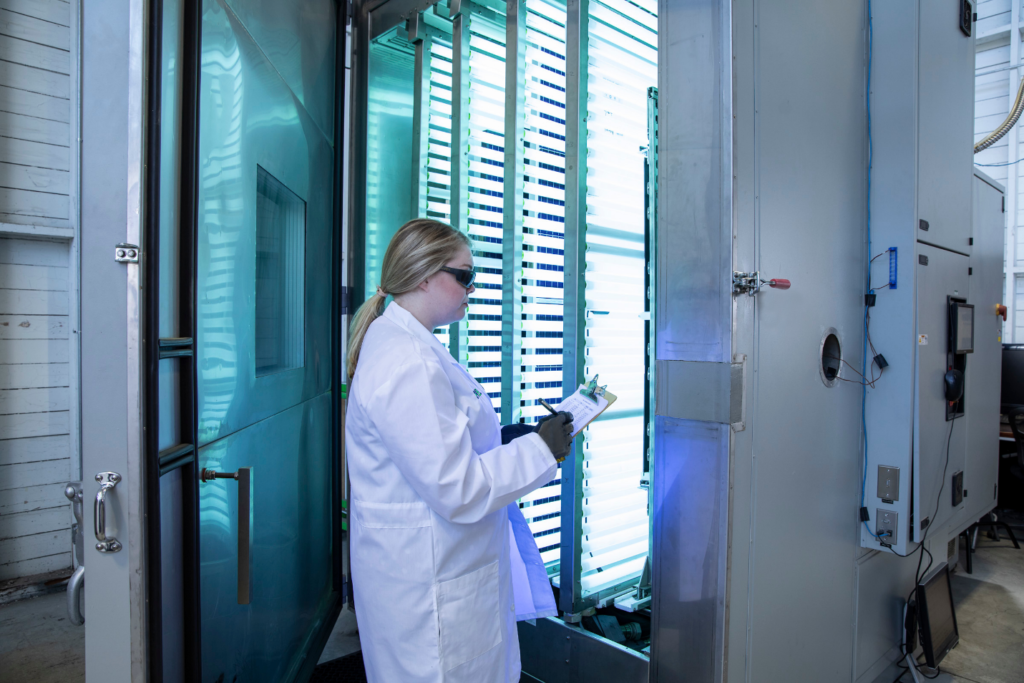
Above, backsheet durability testing at PVEL’s Berkeley lab. UV light chambers are used to simulate exposure to sunlight.
Changing Factories and Production Processes
Here at PVEL, we’ve also observed coronavirus impacts on factory audits, factory witnessing and production oversight. According to Ian, “Change is the devil for quality and things have been changing. We’ve experienced shifting of factories, where manufacturers are moving production between locations or to sub-contractors in order to work around the virus.” Factory locations can affect PV module quality just as much as the BOM, so suddenly changing the location of production should be concerning for buyers.
Many of the factories in Southeast Asia employ staff from China in important quality management positions. When these employees went home for the New Year holiday, they were unable to return due to travel restriction, so factories may have operated without typical levels of quality oversight. Some manufacturers also shifted production around their different factories in Southeast Asia to keep up with demand, and PV module buyers ended up purchasing products made in different locations than they expected. PI Berlin ramped up its production oversight operations in Southeast Asia to ensure that PV module buyers could be confident in product quality even though circumstances had changed.
While most factories in China are reportedly back to full capacity, production has now tapered in Southeast Asia, India and other manufacturing hubs. It may be possible to shift production back to China – but can factories maintain the same level of quality when they’re operating around-the-clock? It depends on the factory, but when production is overseen by an audit firm like P.I. Berlin, buyers can protect themselves from potential issues.
Batch Testing to Mitigate Procurement Risk
Whether the procurement challenge is a new BOM or a new factory, batch testing PV modules as they are produced is a critical risk mitigation tool. With batch testing, a statistical sample of the PV modules produced for a project is sent to PVEL directly from the factory.
We quickly conduct mission-critical performance and reliability tests so that major safety and quality issues can be identified. Batch testing can include:
- Serial Defect Testing: verifying compliance to IEC 61215
- Potential Induced Degradation (PID) testing
- Light Induced Degradation (LID) measurement
- Light and elevated Temperature Induced Degradation (LeTID) measurement
- PAN file measurement
- Incident Angle Modifier (IAM) coefficient measurement
- High Throughput Module Inspection (HTMI): Flash, EL, and visual inspection by the hundreds of modules or by the container load
Any problems PVEL identifies are immediately shared with the buyer so that they can be remedied.

Above, flash testing at PVEL’s lab in Berkeley, CA. Comparing degradation before and after a stress test gives buyers the information they need to determine if the statistical sample meets expectations.
Pricing Uncertainty and Compressed Timelines
The market is currently in a state of flux. Companies up and down the PV value chain must contend with tremendous uncertainty. Based on PV module manufacturers’ preexisting capacity expansion plans and the likelihood of softening global demand, there is a good chance that PV module prices will drop. It’s possible that prices of inverters and other balance-of-system equipment will too.
Market research firms such as Wood-Mackenzie and IHS Markit have already reduced their solar market growth predictions for 2020. Deadlines for key financial incentives have been delayed in some markets. In others, the deadlines remain substantially in effect, so permitting delays and construction shutdowns may make it impossible for developers to meet eligibility timelines for incentives.
Does it make sense to procure equipment in this time of uncertainty? How can financiers and asset owners protect their investments if construction is rushed?
The costs and benefits of changing procurement timelines to leverage lower prices depend on the particulars of each project. If a project depends on time-sensitive financial incentives, waiting to procure modules at lower prices could ultimately cost more than buying now.
PVEL provides project-specific guidance to developers based on our proprietary technology and cost research. Our quarterly Solar Technology and Cost Forecast reports, produced with support from our partners at Exawatt, will cover the expected impact of COVID-19 on PV module pricing in detail. These quarterly reports forecast the cost, price, power and form factor of PV modules on a three-year basis.
For projects that must proceed on schedule, construction timelines could be compressed for many reasons, such as factory shutdowns, shipping issues and permitting delays. Some local authorities are restricting construction activities due to shelter-in-place orders. Rushing construction or bringing in less-skilled workers to ensure that COD, or commercial operation date, does not slip can be risky. Some developers may have no choice.
To protect themselves, asset owners can leverage PVEL’s field testing services when systems are commissioned. By conducting field EL imaging and capacity testing, site owners can validate that construction meets their quality standards. These tools ensure that product defects and poor construction are identified before product and workmanship warranties expire.
The Bottom Line: PVEL’s Best Practices work – rain or shine!
Project developers, investors and asset owners are right to be concerned about PV equipment procurement and accelerated construction timelines. The situation on the ground in factories and project sites around the world is changing quickly. However, PVEL’s best practices for quality assurance remain constant, especially when faced with the uncertainties resulting from COVID-19.
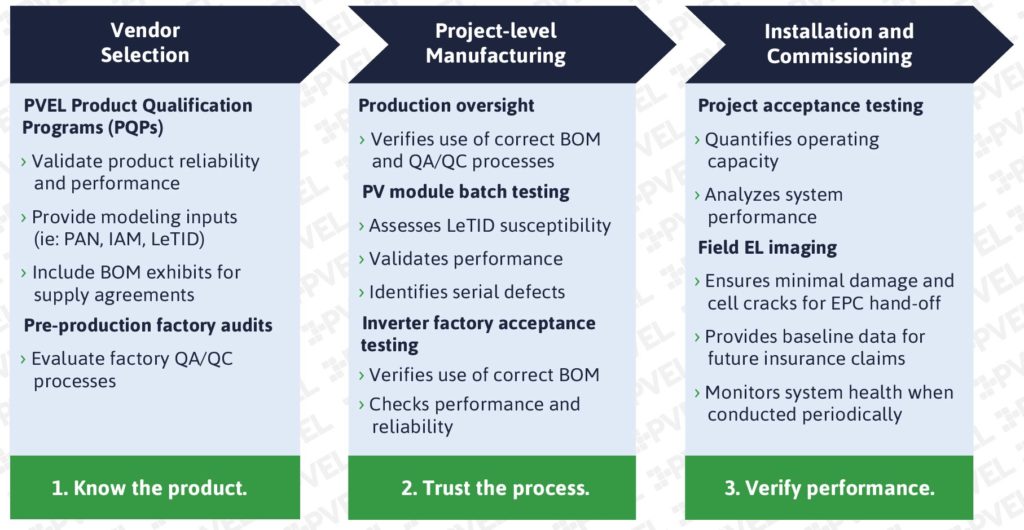
The chart above outlines PVEL’s recommended technical best practices at each stage of the project.
Solar project developers, investors and EPCs can protect themselves by taking a few key technical due diligence steps that PVEL and our factory audit partners recommended before the international pandemic. Our lives and our businesses may be changing in many ways, but PVEL will continue to recommend these best practices long after we see the sunshine at the end of the coronavirus tunnel.
Interested in procurement support, batch testing or field testing? Contact Andrew Sundling at andrew.sundling@pvel.com.